Priducts
PE

Two Stage Screw Compressor
With PM Motor (VSD)
Keeping your production up and running
kimair. compressors ensure long and trouble-free lifetime at the lowest operating cost.
Reducing your production costs
The innovative design of kimair compressors reduces your energy bill and overall
compressor life cycle costs.
Two stage Air Compressor
The bearing load is greatly reduced.Improved Air-end longevity.Reduced maintenance.
2-stage air compressor can set the pressure ratio of three to one between first and second stage so that
it can reduce internal leakage, and each pressure ratio of the 2-stage air-end is much lower than that of
single stage air-end. So it improves pressure efficiency significantly.
After compression of air in the first stage, the air is cooled down
by intensified oil injection cooling which reduces the intake air
temperature of the second stage. As the results, the process of air
compression is done by isothermal compression which can reduce
energy consumption.
Through the optimization of volumetric efficiency and adiabatic
efficiency, 2-stage air compressor can be obtained 15% more air
volume compare to the same power of single stage air compressor

PS

Single Stage Screw Compressor With PM Motor (VSD)
Another breakthrough for kimair company with the new K-PS series.
PM Motor has no motor bearing and make 100% transmission efficiency.
Especially low energy consumption, the noticeable quiet running and extremely
easy maintenance are the results of a totally new design.
PM Motor
has no motor bearing and make 100% transmission efficiency.
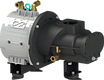
PLE / PLS

Application Scope
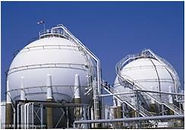

Low Pressure Screw Compressor With PM Motor (VSD)
Cost Saving by kimair. Low Pressure Compressor
Normally in the industries such as textile, cement, chemical fiber and glass production,
required pressure for air is lower than 5bar. kimair Low pressure compressors which
are available for providing low pressure range 2~5bar with much increased air flow
compared to 7~8bar normal compressors enable customers to have remarkable cost
saving up to 30%.
Fully redundant oil and air separation
treatment system.
Large displacement air compressor is more suitable for dual oil and air separater tank
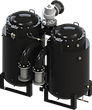



The new K-PL series has already passed the test runs in real conditions with flying colors.
As diverse as the operating conditions may be – its robust technology, low maintenance needs and the
pioneering achievements to maximize efficiency will let it quickly win over friends wherever a reliable
compressed air supply is indispensable.
kimair. Low Pressure Mechanism
Through application of big rotor and direct connection between motor and air-end , it is able to achieve
low speed running and ensure high performance.
And kimair unique design of air oil separator tank guarantee the outlet oil content less than 3ppm or even equal.

Optional online maintenance system
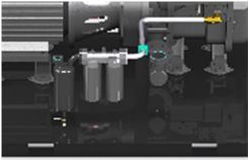
Air compressor lubricating device.
Temperature - free valve design .
reduce the failure point.
SFPS / SFVS
Water Lubricating Oil free Single Screw Air Compressor
kimair ® K-series oil free single screw air compressor use water for lubricating.
The water after filter system can satisfy the drinking water standard so the
air compressor can output clean compressed air.
Water in oil free compressor achieves the effect of lubricating, cooling,
sealing and noise reduction. Water also facilitate the ideal isothermal compression process.
The discharged water require no special treatment which is environmental-friendly.
Best energy saving and lowest maintenance cost
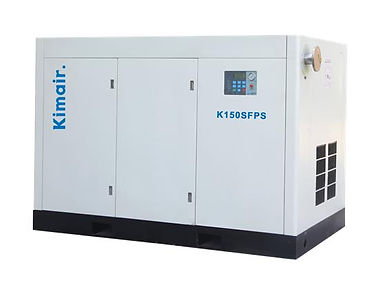
Single screw is widely used in
air compressor. It consists of a single main screw and two vertically-aligned star wheels. The rotator is uniform loaded, and the two star wheels are symmetrically positioned around the axial of main screw.
The dynamic balance achieved by this scheme can reduce the load of screw and reduce the working noise.
kimair ® provide clean, oil-free and pollution-free air compressor, the zero emission pollution treatment can effectively protect the environment.

For low temperature compression
(45 degrees), easy line filter and water changes.
Production of low temperature clean air supply. No oil is used so no need for waste oil treatment. The permanent magnet motor is adopted to make the rotating speed change faster and the efficiency is higher than the induction motor, so the efficiency of the air compressor is greatly improved.
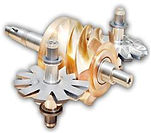


Quietness
Without thrust load on the axis direction of the rotor, the force in the circumference direction rotates quietly with good balance. As a result, the load on the bearing is reduced, minimizing the generation
of noise or vibration.
Durability
The gate rotors follow the rotation of the screw rotor along its gear.
The water film formed on the screw rotor's gear and the free floating mechanism maintain the high efficiency for a long working period.
High Efficiency
Since the lubrication water is jetted during the compressing process,
the compression is done smoothly under almost even temperature, realizing ideal, safe and highly efficient compression with slow rotation.
Stable Air Delivery
Depending on the valve of pressure sensor,
the digital controller change the motor rotation
speed through inverter. That is how it controls
The discharge air pressure to make stable air output.